Best Practices for Enhancing Quality in Sheet Metal Punching and Welding
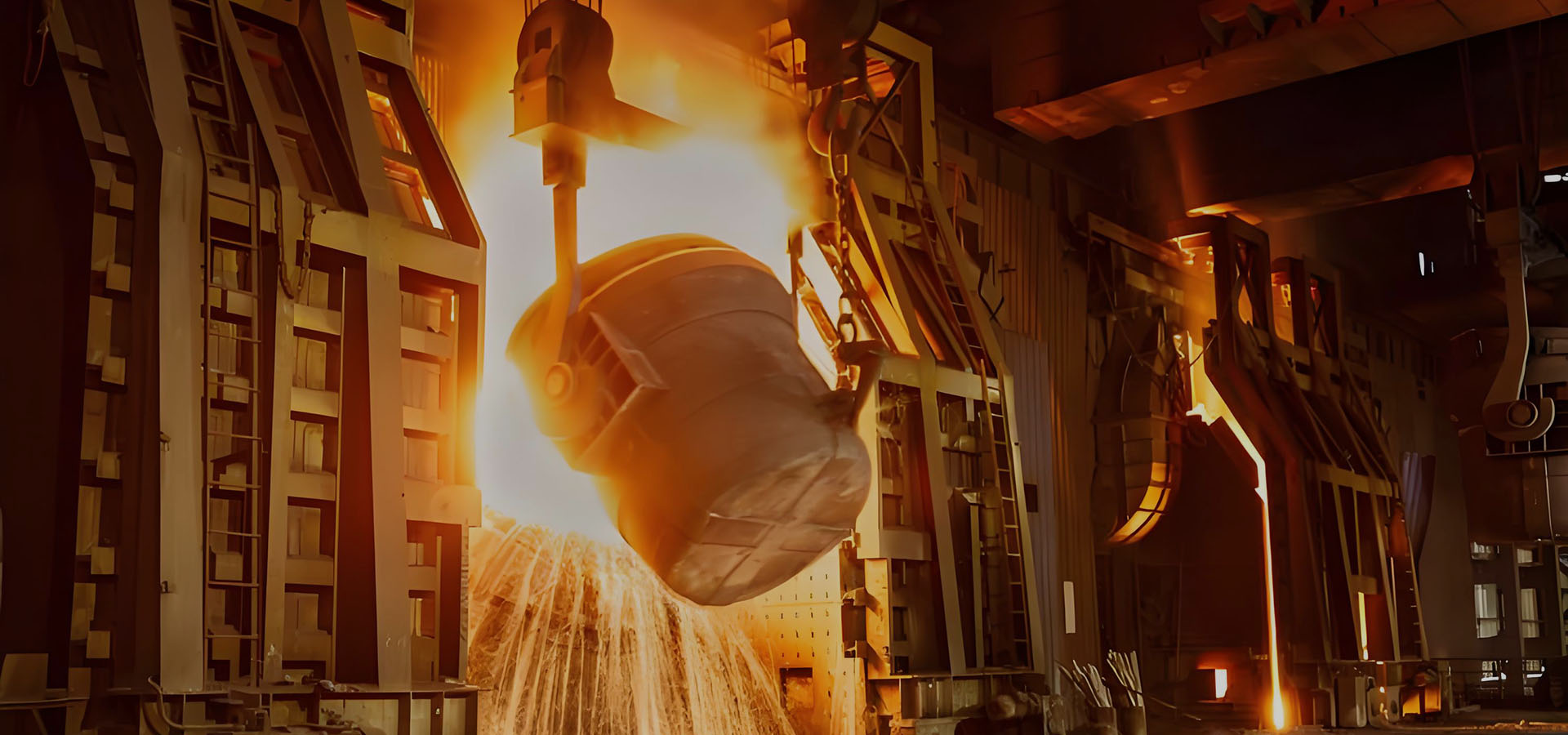
Sheet metal punching and welding are integral processes in modern manufacturing, used to create everything from automotive parts to consumer goods. Achieving high-quality results in these processes is essential to ensure durability, performance, and cost-efficiency. In this blog, we’ll explore the best practices for enhancing the quality of sheet metal punching and welding, helping manufacturers optimize their operations and deliver superior products.
1. Choose the Right Materials
The first step in ensuring quality in sheet metal punching and welding is selecting the right material for the job. Sheet metals come in various grades, thicknesses, and alloy compositions, and each type has its own properties that affect how well it responds to punching or welding.
- For Punching: Material thickness, hardness, and ductility are crucial factors. Materials like mild steel, aluminum, and stainless steel behave differently under the punch press. Choose materials that offer a balance of strength and flexibility to avoid excessive wear on tools.
- For Welding: Material compatibility is vital for a strong bond. Ensure that both pieces being welded are of compatible material types to prevent issues like poor fusion or weakened joints.
2. Invest in High-Quality Equipment
High-quality punching and welding machines play a crucial role in the outcome of the process. Regular maintenance and investment in advanced machinery help improve the precision and consistency of each part produced.
- Punching Machines: Precision is key when punching sheet metal. A modern CNC (Computer Numerical Control) punching machine allows for high accuracy, reducing the chances of defects such as uneven holes or tool wear.
- Welding Machines: For welding, advanced MIG, TIG, or laser welding machines can help achieve cleaner, stronger, and more precise welds. Make sure to use equipment that suits the specific requirements of the material and joint design.
3. Optimize Tooling and Dies
The choice of tools and dies is crucial in sheet metal punching, as they directly impact the quality of the punched holes and shapes. Proper tool maintenance and selection can drastically improve the quality of the end product.
- Tool Maintenance: Regularly inspect and replace worn-out tools to avoid deformations, burrs, and imprecise cuts. Dull tools can increase the risk of defects and affect material quality.
- Die Design: Ensure that your punching dies are designed for the specific job. The right die configuration can reduce the occurrence of burrs, material distortion, or tearing.
4. Control the Punching Process Parameters
For optimal punching results, it’s essential to control various process parameters such as pressure, speed, and clearance.
- Pressure: The punching force should be adjusted based on the material type and thickness. Too much pressure can deform the material, while too little can lead to incomplete punches.
- Speed: Punching speed affects the accuracy and efficiency of the process. Ensure that the machine speed aligns with the material’s behavior under stress.
- Clearance: The clearance between the punch and die affects the quality of the punched hole. Too little clearance can cause excessive burrs, while too much clearance may result in poor hole formation.
5. Focus on Joint Preparation in Welding
Before welding, proper joint preparation is crucial to ensure a strong and clean weld. Improperly prepared joints can lead to weak bonds and defects such as incomplete fusion, porosity, or cracks.
- Edge Preparation: Make sure the edges of the sheet metal are clean, smooth, and properly beveled, especially when working with thicker materials. This helps ensure a deeper penetration and stronger weld.
- Cleanliness: Remove any dirt, oil, or rust from the surfaces to be welded. Contaminants can weaken the weld and cause defects like porosity.
- Fit-Up: Properly align the parts before welding. Misalignment can lead to stress concentrations and affect the overall quality of the finished product.
6. Control Heat Input in Welding
Excessive heat input during welding can lead to warping, distortion, or weakened joints. It’s crucial to control the heat during the welding process to ensure consistent results.
- Welding Speed: Adjust welding speed to ensure proper heat input. Too slow of a weld can result in overheating, while too fast can lead to insufficient penetration.
- Cooling: Allow the welded part to cool gradually and uniformly. Rapid cooling can cause residual stresses and lead to cracking.
7. Conduct Thorough Quality Control and Inspection
Quality control should be an ongoing process in sheet metal punching and welding. Regular inspection ensures that any issues are caught early, preventing defects from reaching the customer.
- Punching Inspection: After punching, check the holes for cleanliness, precision, and burr formation. Use calipers and micrometers to measure hole dimensions accurately.
- Welding Inspection: Post-weld inspection should include visual checks for defects, such as cracks, porosity, and distortion. Non-destructive testing (NDT) methods like ultrasonic testing or x-ray inspection can be used to detect internal defects.
8. Post-Processing and Finishing
After punching and welding, the parts often require post-processing to achieve the desired finish and remove any defects.
- Deburring: Remove burrs and sharp edges from punched holes. This can be done manually or with automated deburring machines.
- Welding Finishing: For welded parts, grinding or polishing may be necessary to remove excess weld material and smooth out the surface. This improves both aesthetics and functionality.
- Surface Treatment: Depending on the application, consider applying coatings such as powder coating, galvanization, or anodization to improve corrosion resistance and finish.
9. Training and Skilled Workforce
One of the most important factors in ensuring quality is the skill of the workers. Well-trained operators can identify potential issues early and adjust processes accordingly.
- Operator Training: Invest in training programs for your workforce to ensure they understand the intricacies of punching and welding, including machine setup, process control, and safety protocols.
- Continuous Improvement: Encourage a culture of continuous improvement by regularly reviewing and refining practices. Employee feedback and lessons learned from past jobs can contribute to higher quality standards.
Conclusion
By implementing these best practices, manufacturers can significantly improve the quality of their sheet metal punching and welding processes. High-quality materials, advanced equipment, proper process control, and skilled workers all contribute to achieving superior results. Ultimately, a focus on quality at every stage of production will lead to stronger, more durable products and a more efficient manufacturing process, helping businesses stay competitive in today’s demanding market.